As this year comes to an end and we look toward the new one (as well as a new decade!), you may be making decisions on changes that will impact your bottom line in 2021. One of the most impactful ways to do this is by considering green manufacturing processes and practices. Not only will these changes create a smaller imprint on the Earth’s energy reserves and limited resources, but they will also likely save you money, too.
The question of how to make manufacturing more eco-friendly is going to be a big one in the coming decades, especially as end-users increasingly demand products with transparent supply chains and smaller ecological footprints.
Here is a list of five changes to consider.
Consider Technological Advances
Over the last few years, several new technologies have been introduced to manufacturing that allows design and prototyping to happen off the manufacturing floor. Using VR or AR technologies to evaluate designs or process changes will help limit waste in the real-world environment. These technologies allow your design team to start over or back up in their design process without any lost product.
Once a digital design has been perfected and analyzed on your virtual platform, you can move it to real-world prototyping, and then to your manufacturing line. Other advances like machine learning can improve your plant’s workflow by limiting downtime, improving your supply chain, and suggesting better use of human labor.
Go Paperless to Help the Environment
Companies like Tesla–the king of green manufacturers–have thrived with paperless environments, relying instead on sets of visual work instructions. This change creates a significant environmental impact, but more importantly, it tends to improve quality and boost productivity. When instructions are relayed electronically, there’s no chance a worker will accidentally pull from an incorrect revision or out-of-date work order since these disappear with every update. Fewer mistakes mean less wasted material and lower scrap rate; that lower scrap rate will have a significant impact on your costs.
Add Renewable Energy to your Plant
The cost of installing solar panels has fallen in the last decade from $8.50 to less than $3 per watt. Additionally, solar panels have an average lifespan of twenty years. Once installed, the cost of upkeep is minimal.
The US Government recently amended the Taxpayer Certainty and Disaster Tax Relief Act of 2020. This extends the Business Energy Investment Tax Credit (ITC) on small-wind projects to 2023.
New Eco-friendly turbine blade materials
Additionally, new additive manufacturing technology allows wind power to increase its ecological punch by 3D printing blades using an advanced thermoplastic resin. This option decreases the cost of wind turbines while also limiting the number of decommissioned blades ending up in landfills. This option is in development as part of a partnership between GE, NREL, and Oak Ridge National Laboratory.
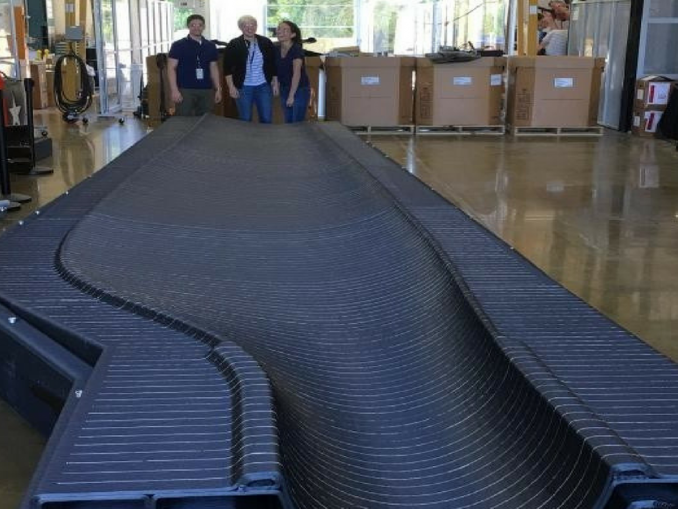
While it is unlikely solar or wind power will ever fully replace traditional energy sources for your plant, the addition of renewable energy as a resource will provide your company with long-term energy security regardless of the price and availability of fossil fuels, and help you become more environmentally friendly.
Consumers are now considering the environmental impact of their purchases from production to end-use; such a change will make your products more attractive to some.
Develop Industrial Symbiosis
Industrial Symbiosis reduces final waste products by creating partnerships between companies where one company’s waste product becomes a resource for the other. This reduces costs for both the upstream and downstream manufacturers. Manufacturers often share facilities, energy, and water costs, further reducing costs.
Conduct an Energy Audit
Your plant should conduct an energy audit every few years. An outside specialist or a knowledgeable internal employee can take care of this. The audit will help identify any areas within your facility that need attention to improve efficiency. Thoroughly inspect lighting, HVAC, and production equipment to identify any usage issues. You can implement conservation procedures once issues are identified.
Don’t forget to share this post!
You must be logged in to post a comment.