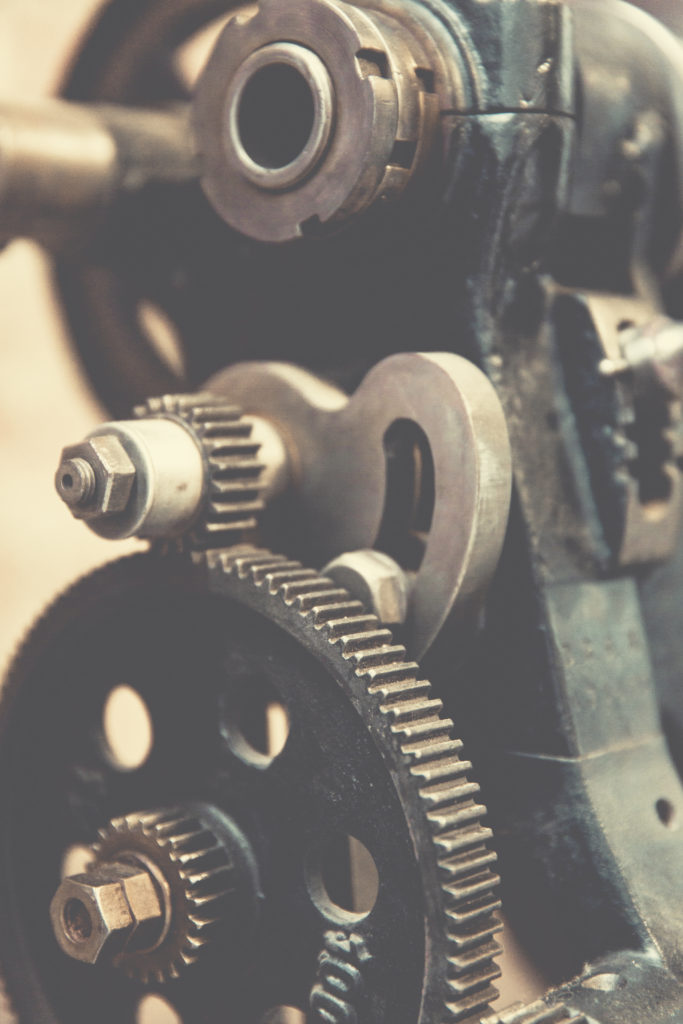
Unplanned downtime due to equipment obsolescence.
It’s a dirty subject no one wants to talk about. And for good reason. A 2016 study by the Aberdeen Group put downtime costs across industries at a whopping $260,000 per hour, up 60% from 2014 data. A 2014 Gartner study was even worse: placing the average cost at $336,000/hour. One lost eight-hour shift could mean a $2.08 million to $2.68 million loss.
Regardless of who’s right about the costs, eliminating downtime and disruption is a high priority for most businesses. Yet more than two-thirds of companies don’t have a full understanding of when their equipment should be maintained, upgraded, or replaced.
While we’re excited about the future of Industry 4.0 and IIoT, where every machine can self-analyze its needs and tell you what to do before there’s a problem, we also understand most factories and industrial locations aren’t there yet. They likely won’t be for decades as they continue to operate with older systems in place.
But old doesn’t mean unusable. Here’s why.
The Why: All industrial equipment becomes obsolete.
The newness wears off, no matter what it is. This holds true whether you’re talking about cars, or furniture, or even people. Things in the physical world break down over time. That’s entropy, a constantly occurring force in natural and mechanical systems.
It’s the same with industrial parts. All machinery will eventually become obsolete. All parts will wear out and need to be replaced. However, due to the natural robust quality of industrial components, usefulness continues until late stages of the life cycle.
This means the average user can reap maximum benefits and value from early capital investments through the implementation of a structured obsolescence strategy that maintains equipment performance and efficiency for as long as it makes sense to do so.
The How: Understanding the price lifecycle
You must first understand parts and their replacements/spares have a price lifecycle.
Industrial parts are sold at their original fair market value from the OEM (original equipment manufacturer). As equipment moves through various OEM obsolescence stages like final new system builds, to repair/spare support, to limited repair or replacement, and on to final obsolescence, the price of parts may begin to rise as demand increases and supply limitations change the market. Over time, prices should again fall as legacy systems are replaced with newer technologies and more parts become available on the market again.
But the timing for this late state price drop depends upon the true lifecycle of the system. This can be different than the equipment manufacturer’s stated lifespan. GE Speedtronic systems (Mark I, Mark II, Mark IV, Mark V, and Mark VI) offer a good example between the two. While each system was developed as though users would upgrade to the next available system after a decade, according to PowerMag.com, no panel “has ever been decommissioned for lack of parts or services. With adequate planning and a sound maintenance strategy, TCPs are safe to operate for as long as required.” (1) And some of them have been; there are Mark I and Mark II systems that have been in continual use since the 1970s or earlier.
A good equipment obsolescence strategy saves money
You can begin to understand why having a good obsolete parts strategy from the beginning can help save money in several ways:
- Avoid buying parts when prices are highest.
- Buy spare parts for backup inventory when prices are favorable, rather than during a time-critical period due to work stoppage.
- Identify your most important assets and assess the risk of obsolescence in specific quantitative/qualitative terms.
- Understand suppliers’ End of Line plans ahead of time to minimize the impact and risk of discontinued support.
- Avoid more expensive long downtimes due to lack of part inventory on hand when demand exceeds availability.
The When: Should equipment be upgraded?
First, we need to understand whether we’re talking about whole-plant upgrades or spot upgrades.
In the case of spot upgrades, in some cases there are new third-party components designed to take the place of OEM obsolete parts. It’s important to understand some of these components may vary from OEM components in some very small but important way that could increase the length of your downtime due to incompatibility. However, if quality OEM parts are not available, third-party parts may allow you to get back running until you’re able to source an OEM replacement.
Embarking on a whole-plant upgrade without extensive research and planning is never recommended. New equipment is one of your largest investments that should result in better reliability, increased throughput, increased security, and a reduction in operating costs due to a drop in energy consumption and overall increased efficiency.
- https://www.powermag.com/comparing-gas-turbine-life-to-turbine-control-life-what-you-need-to-know/
You must be logged in to post a comment.