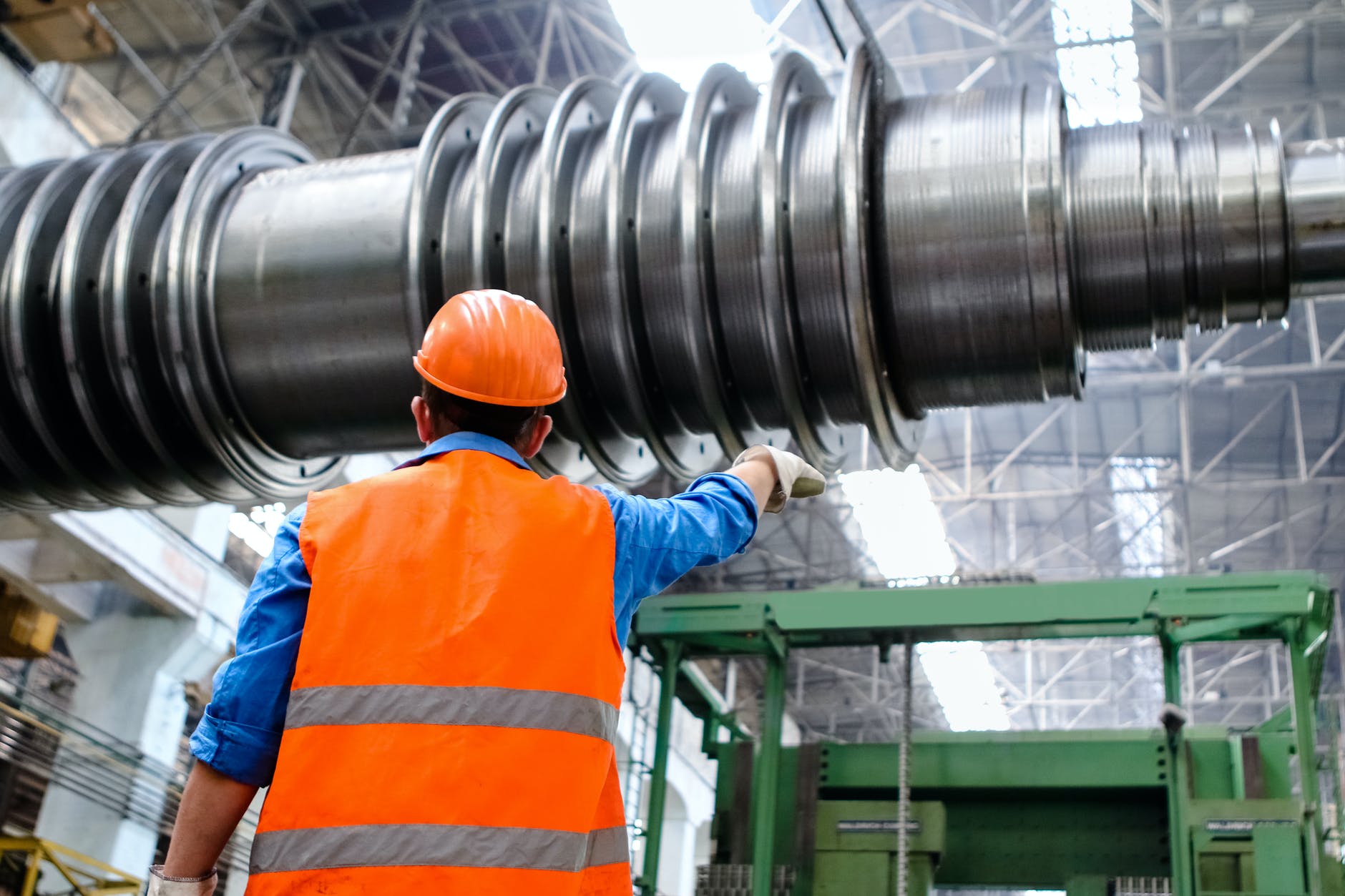
According to Hubspot’s Annual Manufacturing Report, 80% of manufacturers feel smart technologies and a move toward Industry 4.0 adoption will benefit their supply chain by increasing visibility, accelerating innovation, and enabling staff to work more efficiently. Over 90% of those polled feel the same technologies will lead to increased productivity.
This begs the question: if smart technologies are essential to efficient manufacturing, why aren’t all factories smart?
It’s not that simple.
Upgrades come with significant costs and productivity ramifications. It doesn’t make sense to pull out legacy equipment in good working order simply because it wasn’t built in the age of connectivity. Many systems continue in good working order for decades; that’s why we use the term “industrial-strength” to define something that safeguards against failure.
Additionally, a full swap to new systems means extended downtime. This is never a good thing for any factory floor. In fact, a recent Garvey study placed the average cost of a single hour of downtime across all businesses at $260,000.
But options still exist. Plant managers wanting to improve their manufacturing supply chain can look to other methods besides replacement to move toward Industry 4.0 implementation. Smart technologies offer many options.
IoT Retrofit Options
Some industrial automation suppliers now offer retrofit solutions that integrate with existing equipment, allowing older machines to communicate data within the larger network. This occurs with few or no changes to existing hardware or software.
Such retrofits add connectivity to existing machines, allowing remote control and monitoring. Such integrations allow plant managers to identify bottlenecks or other areas where inefficiencies are occurring.
With accurate data measurements of temperature, vibration, power, and current consumption, the performance of connected equipment is automatically determined. Real-time operation analyses lead to increased visibility. This can lead to increased productivity similar to that of a full equipment upgrade, without the associated costs.
Manufacturing Supply Chain Ramifications Up and Downstream
Real-time insights on the factory floor have ramifications not only for the plant itself, but also for upstream and downstream partners. According to one 2019 Deloitte study, manufacturing figures into one-third of GDP and employment, in one way or another, within the USA. Better visibility on the factory floor allows for near-to-real time scheduling of goods from upstream partners while maintaining the proper supply chain for delivery to downstream partners, with improved control, leaner inventory, increased agility, and reduced capital expenditures.
Conclusion
Smart manufacturing maturity is coming. Unfortunately, it won’t happen overnight. Adding IoT connectivity to existing legacy equipment offers an opportunity to stair-step into the future. This maintains working equipment and builds connectivity into it. By taking this approach, managers can mitigate risk while still moving forward with a twenty-first-century digital transformation. It’s an important step in improving factory performance and maintaining a competitive edge.
If you need to know more about how to bring your legacy equipment into the IIoT age, we’ve written about that.
Need help sourcing replacement parts for your legacy systems? We can help.
You must be logged in to post a comment.