When I was in my mid-twenties, I ran an in-store optical lab for one of the big national “in an hour” eyeglass chains. It was a fun but demanding job. Sometimes the lab was understaffed, and meeting those hour deadlines got tight.
One day, as I was trying to cut a few seconds off the time grinding a lens, I reached into the curve generator to move the lens to the next machine while the diamond cutting blade was still spinning–something I knew we weren’t supposed to do–and heard and felt a sudden ppzzt! as the spinning blade made contact.
Luckily for me (maybe), the blade had hit my diamond engagement ring instead of my hand, ruining the stone.
I never reached into the moving machine again. I also stopped wearing jewelry to work.
M Kenney–tech writer, AX Control
Provide Safety for Your Employees
No matter what industry your manufacturing plant is part of, providing for the safety of your employees has to be a top priority. Compliance with safety regulations prevents your workforce from accident or injury. It also keeps you from dealing with costly OSHA violations and with their ramifications, which often mean expensive shutdowns.
Proper training and implementation will help you avoid violations. It’s that simple.
But violations are also simple for compliance officers to spot. In fact, most of the top 2020 violations have been leading OSHA violations for years, some for over a decade.
But what if employees misunderstand your safety goals? Are you being clear and consistent with your expectations? You’re going to have to do more than tell your employees to follow the rules once(see above about the ring) if you want a safe work environment.
Here’s a list of the seven most common OSHA violations in industrial/manufacturing settings. We’ve included tips on how to keep your team from making them.
Fall protection (29 CFR 1926.501)
Falls are, overall, the third-leading cause of death and the second-highest cause of workplace injury. It also accounts for 12 to 15% of all Workers’ Compensation costs. While the majority of these accidents occur in the construction industry, a significant number still happens in manufacturing.
Most Cited OSHA Violations of 2020–All Locations
1. Fall Protection – General Requirements
2. Hazard Communication
3. Scaffolding – General Requirements
4. Control of Hazardous Energy – Lockout/Tagout
5. Respiratory Protection
6. Ladders
7. Powered Industrial Trucks
8. Fall Protection – Training Requirements
9. Machine Guarding– General Requirement
10. Personal Protective and Lifesaving Equipment – Eye and Face Protection
To avoid problems with OSHA, keep walking surfaces clean and free of clutter. Inspect lighting and signage, and make sure both are adequate in all areas of your plant. Additionally, require safety footwear in hazardous areas.
Finally, have a semi-annual, quarterly, or monthly plan in place to inspect any areas of your plant that may lead to fall hazards. This includes scaffolds, elevated walkways, ladders, or loading docks.
Hazard communication (29 CFR 1910.1200)
A Hazard Communication Plan, required by OSHA, keeps your employees safe from chemical hazards. It also ensures they handle chemicals without posing a hazard to others. A communication plan is a written program utilizing Material Safety Data Sheets (MSDS), labels and warnings, and a comprehensive hazard communication training plan.
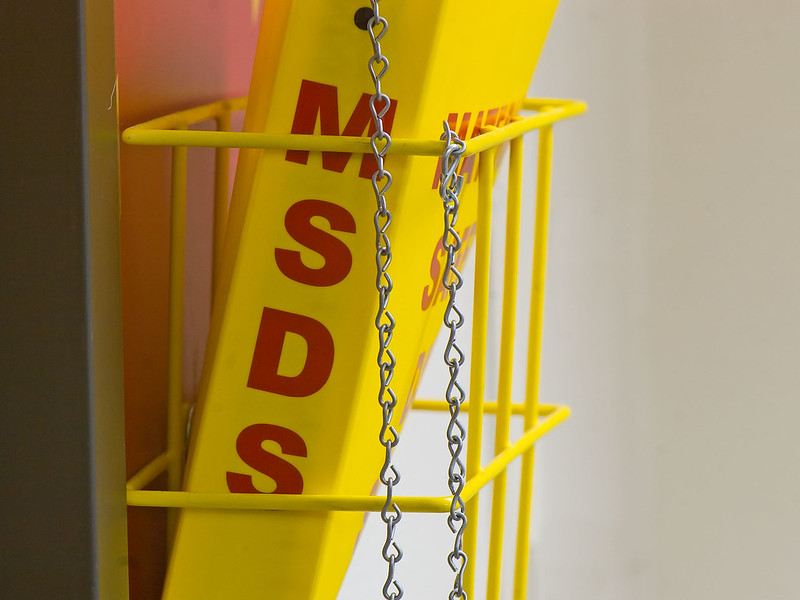
Avoid OSHA violations by maintaining proper MSDS documents. Post warning signs, first-aid, and fire-fighting measures where needed. Maintain a written inventory of all chemicals with proper container labels. Train employees on chemical hazards and precautions. Training updates should occur as needed.
Respiratory protection (29 CFR 1910.134)
Improper use, lack of use, or simple ignorance of this code has kept this code in the top ten for years.
Approximately 5 million workers across 1.3 million workplaces should wear a respirator during some or all of their work shifts. Yet over 2 million people are diagnosed with cancer each year after prolonged exposure to workplace carcinogens. Proper respirator use would significantly reduce exposure and likely drop associated cancer rates.
Identify and evaluate respiratory hazards in your plant, then provide the proper personal protective equipment to employees who need it. Train employees in equipment care, cleaning, and maintenance. Also, check respirator fit, and ensure employees actually use them by keeping written compliance records.
Most importantly, evaluate each employee to ensure they are healthy enough to wear a respirator before use in your facility. More violations are written due to a lack of this medical clearance than any other part of this regulation.
Control of hazardous energy (lockout/tagout) (29 CFR 1910.147)
According to OSHA, Lockout/Tagout procedures involve an “authorized employee(s) either locking or tagging the energy-isolating device(s) to prevent the release of hazardous energy and take steps to verify that the energy has been isolated effectively.” Lockout/Tagout ensures machinery is disabled and cannot accidentally be energized during service or maintenance.
It’s easy to avoid Lockout/Tagout violations. However, this relies on training. Violations occur because employees haven’t received proper Lockout/Tagout traning, or don’t understand the risks associated with ignoring these procedures.
Make sure your LOTO equipment is in good shape and is adequate to perform all necessary procedures. Additionally, identify all sources of energy on your equipment and take steps to disable each one. This includes unelectrified sources of energy; remember gravity and kinetic energy also have to be locked out. Identifying all sources of energy is a very important step with new equipment.
Powered industrial trucks (29 CFR 1910.178)
Forklifts or powered industrial trucks pose a real danger to those working nearby. These moving machines can cause serious injury–even death. Unfortunately, the improper use of these large vehicles has consistently ranked in the top ten OSHA violations.
Make sure your plant has clear written rules and restrictions for how, where, and when forklifts can be used. All operators should hold appropriate licensing. Don’t allow employees lacking proper credentials to operate equipment, even for a moment. A training program should be in place to help cement these rules.
Machinery and Machine Guarding (29 CFR 1910.212)
Machine guards are in place to protect employees from sparks, moving parts, and pieces of debris. When machines with flywheels, moving belts, saw blades, or other moving parts aren’t properly guarded, they put employees in harm’s way.
Never remove or compromise an existing guard. Add guards to equipment that may need them. Train workers to use machinery properly with the guards in place, and keep a regular maintenance schedule in order to maintain guard tolerances.
Eye and Face Protection (29 CFR 1926.102)
Many employees require eye and face protection. If a job requires contact with environmental, chemical, or radiological hazards, always provide eye and face protection. Without this equipment–and without the proper training on how and when to use it–employees could suffer blindness, severe injury, or death.
Have a PPE workplace training program in place. Additionally, make sure eyewash stations are available. Post first-aid instructions and procedures nearby, and train employees to know how to implement them.
Be Proactive with safety
OSHA citations carry penalties from a few hundred dollars to $70,000. Proper implementation, training, maintenance, and record-keeping can help you avoid them. Don’t wait for an injury or violation to occur. Make sure you are providing your employees with a safe and secure workplace and you will likely avoid the most common problems. And if/when an accident does occur, you will be less likely to receive a high dollar citation, if any at all.
Did you find this useful? Feel free to share.
Do you need help sourcing older industrial replacement components to ensure your equipment is running safely? We can help. Talk to our team today.
You must be logged in to post a comment.