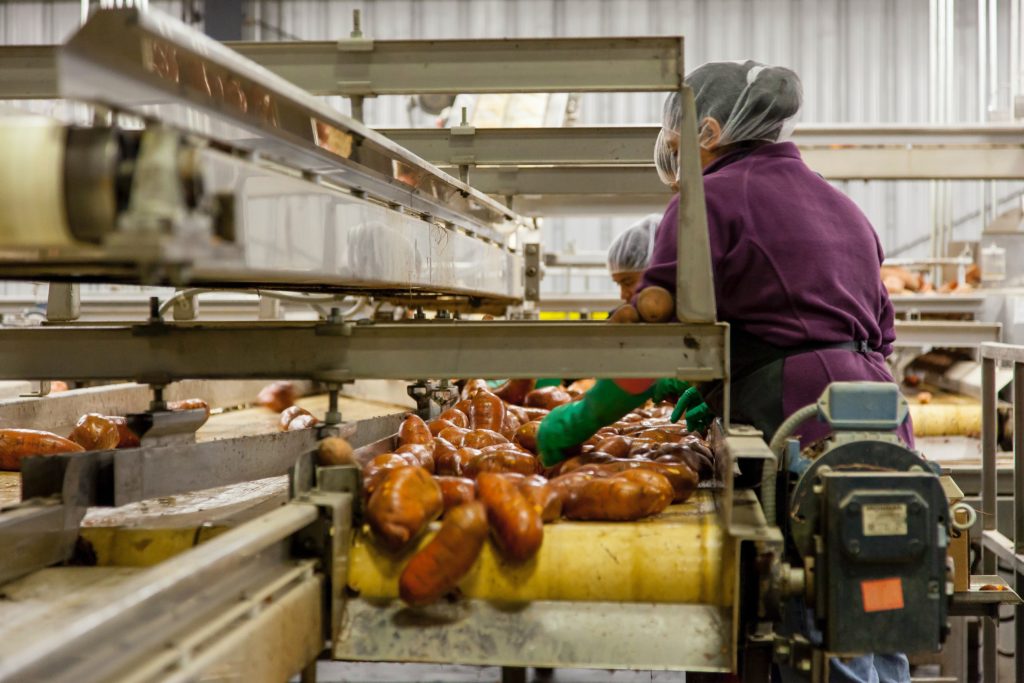
Industrial equipment is expensive. It’s also big, designed to last, and often complex. When you add all those factors together you begin to realize just how much is at stake when it comes to upgrading your facility. It’s too easy to overlook some important aspects of the decision that can lead to regret for years to come.
The list below is designed to help you think about any upcoming purchases in a mindful way to reduce the chance of buyer’s remorse and increase the likelihood of a successful upgrade. It’s by no means a complete list, but it should help you get on your way.
Will the new industrial equipment fit?
While it’s always a good idea to make sure you have the physical space for any new equipment, there’s more to ensuring a good fit than measuring W x H x D. Consider other questions like
- Are my current utilities sufficient to run this equipment?
- Will I need to upgrade security?
- What are the safety requirements to keep my staff protected?
- Have I chosen the most efficient location for this equipment?
Will you buy or lease?
Buying equipment means complete control and ownership of your equipment and an increase to company assets. But buying also means you’re also completely responsible for maintenance throughout the machine’s life cycle. However, in some cases obsolete-to-you can still be valuable to others, allowing you to offset some of the purchase price by selling equipment to a legacy dealer like AX Control when you’re ready to upgrade again. Don’t forget to consider this when you’re comparing lease costs to purchase costs.
Leasing has other benefits and is a popular choice for many. Leasing often expands your budget and options to beyond what you might be able to buy, allowing you to upgrade without loss of cash flow. But leasing one system after another means payments that never end without any payoff. Some lease agreements can lock you into terms that work well for now but may not meet your needs in a few years due to expansion–or contraction–of business. Finally, lease payments rarely end when convenient. This means you can need upgrades again before the lease ends. Or you could still owe for equipment you no longer need due to a changed business model.
What else will you need to buy or upgrade?
Too often in life one purchase leads to many other purchases; this holds true for manufacturing equipment. As you work to interconnect new equipment with existing, consider
- Will this need protection from the working environment, such as from power fluctuations or moisture?
- Will you have to add special safety equipment like safety sensors, fire suppression, or PPE to properly operate your new upgrade?
- What existing equipment will it have to ‘talk’ to? Does it come with the proper network adaptors, USB ports, disk drives, or other connection points to achieve connectivity?
- If your new equipment requires data to operate, how will that data be received, stored, and protected?
Who will use the new industrial equipment, and how often?
Don’t forget to factor in the cost of training when adding new equipment to your floor. You’ll need to consider what kind of training or re-training you’ll need to provide to workers so they can safely use your acquisition. Also think about who will provide this training, at what cost, and what effect the training window will have on your efficiency. The longer training takes, the more significant the effect can be on output.
Additionally, consider how you’re going to use the new equipment. Is this going to be part of your everyday manufacturing process or something that’s used only when needed? Equipment used on a less regular schedule can lead to security and safety risks due to forgotten best practices and missed security updates.
Make sure maintenance expectations are covered, whether your equipment will be used sporadically or every day. If operators are unaware of maintenance schedules and quality checks, or don’t recognize when indicator lights are showing a problem, your new expensive equipment may have a shorter lifespan than you expect.
Finally, don’t forget to consider your new equipment’s end of life. While some equipment is designed for decades of use, you may only get a few years out of other items. With longer life comes increased reliability and cybersecurity risks as the world changes around your older equipment. But short-use items may have hazardous materials that make them difficult to dispose of, or may hold sensitive data you’ll need to consider before removal.
Sell Your Surplus
Remember when it’s time to upgrade to check with AX Control to see what we can offer for your old equipment. See our Sell Your Surplus page for more details.
You must be logged in to post a comment.