Let’s talk about machinery manufacturing.
Machines have come a long way from their humble beginnings. While elementary-school science teachers still struggle to convince students that screws, levers, and wedges truly are machines, the machines we know today have moved far beyond these simple principles.
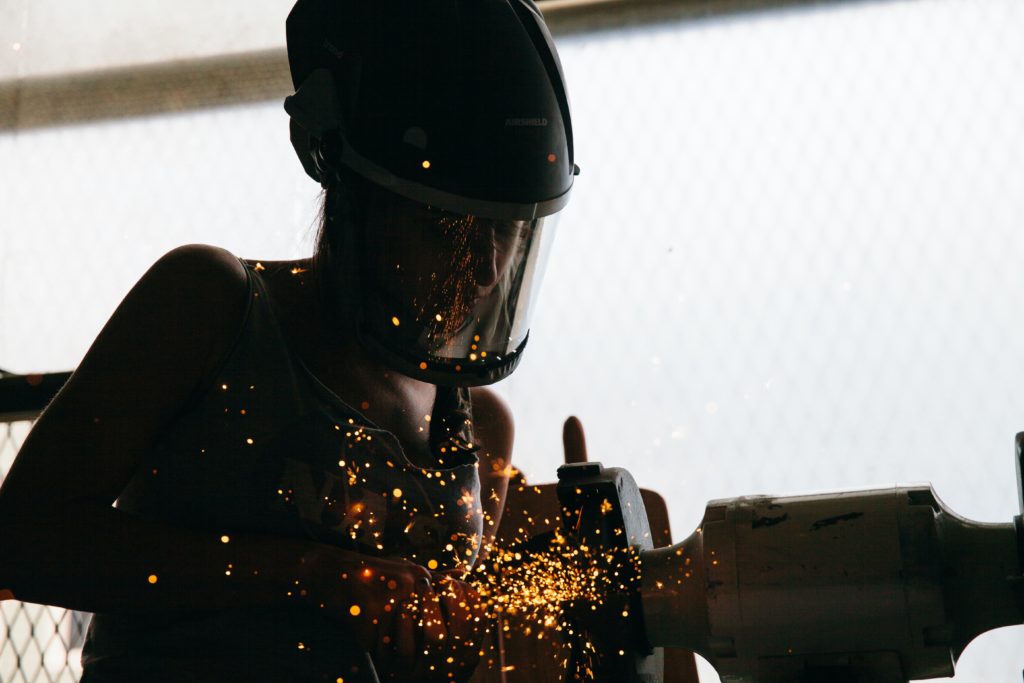
In fact, machinery of some kind is used in almost every modern workplace. Because of their vast reach, machinery manufacturing–which includes everything from engines and turbines to agricultural machines and HVAC equipment–has a significant impact on economic sectors like construction, agriculture, transportation, and power production.
Modern Machinery Manufacturing: How It’s Made
Modern machines rely on multiple manufacturing processes. This includes shaping individual machine pieces through stamping, forging, bending, 3D printing, or machining. This requires tools like lathes, hobbing machines, gear shapers, drilling and milling machines, as well as grinders and planers.
While robotics help with assembly, humans still put together many machine parts due to their complexity. Human hands have the dexterity and precision needed to assemble parts quickly, even better than many robots. Welding plays a big part in the assembly processes, too.
This dependency on human workers means there are plenty of good-paying jobs available within the industry. In fact, over a million American workers find their employment here as machinists, mechanical engineers, welders, CNC operators, and in other positions.
The Changing Machine Manufacturing Industry
Better. Stronger. Faster. Today’s industrial machinery manufacturer has to be all three, just like 6 Million Dollar Man Steve Austin (that’s one for the over-50 crowd.) End-users want products customized for their use, and they want them quickly. This means finding ways to produce small-batch machines (as small as one) in efficient and cost-effective ways.
To do this, machinery manufacturers are turning to technology for help, again like Steve Austin. Automation and robotics both come into play here, but so do less obvious things like adding solar panels to the roofs of facilities to reduce energy costs. Digitalization and the addition of IIoT (Industrial Internet of Things) have also helped improve manufacturing times, increase productivity, and reduce associated costs.
Meanwhile, manufacturers are now jumping on the *aaS trend to benefit from growing industry servitization needs. This pivots their role from parts-supplier to partner, providing customers with reliable warehousing, security, and administrative support.
Smarter Design, Thanks to Technology
Industrial-strength. We use the term all the time. But have you ever thought about the implications of this term?
Industrial-strength: marked by more than usual power, durability, or intensity
Merriam Webster Dictionary
Modern industrial machinery is made to last a long time. For that reason, good design with a full understanding of the product lifecycle is critical to creating reliable and effective products.
Increasingly, machinery manufacturers are turning to virtual modeling (otherwise known as simulation models) to thoroughly check mechanical, electrical, and embedded software systems of a design before building a physical machine.
This kind of digital design system is a potential game-changer for the industry. Now design engineers can look for ways to create machines with built-in flexibility. Thus customers know from day one that as their needs change, their machinery has the potential to adapt to those needs.
Adding New, But Keeping What Works
As we said before, modern machinery lasts a long time. It’s also expensive, and few businesses can upgrade everything at once. So what’s the best way forward?
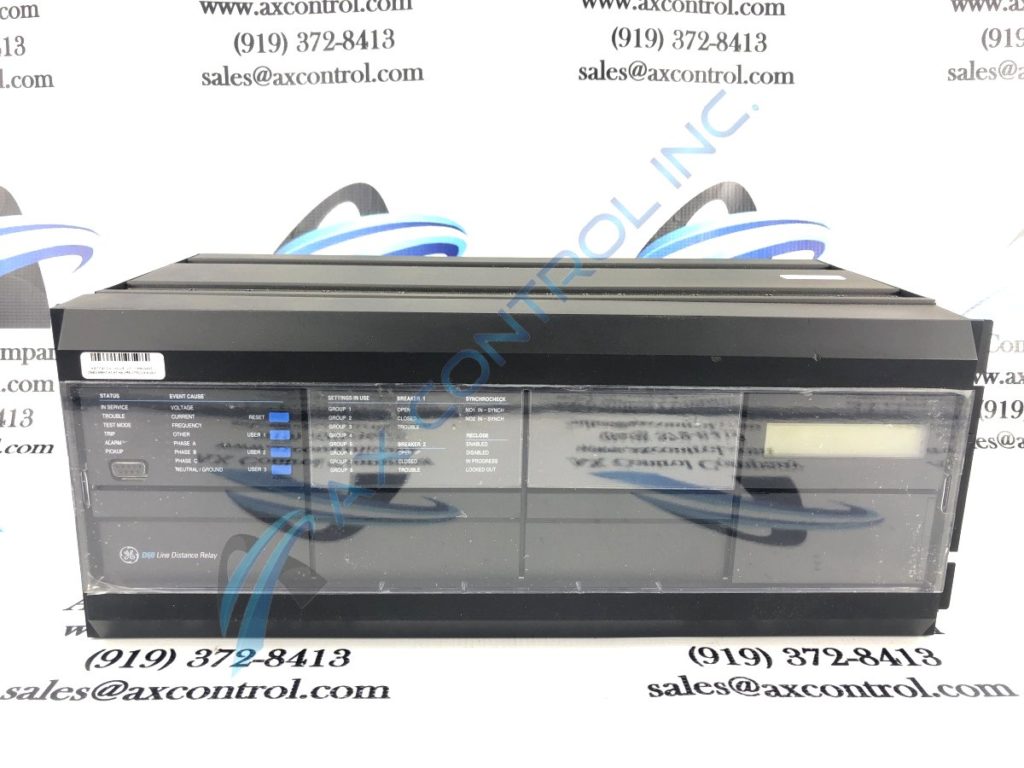
Nothing says everything must upgrade at once. Many companies begin by identifying which machine upgrades will have the biggest impact. When sensitively designed, newer systems should improve overall production capabilities as well as reliability and quality.
However, manufacturers and end-users need to make sure new equipment will integrate seamlessly with in-place legacy systems. Otherwise, quality improvements will be impacted or lost altogether.
A technological assessment of all equipment can help determine how to achieve this. Web services can apply to many older applications, increasing connectivity. Also, middleware applications like data access layers (DALs) or application program interfaces (APIs) can improve performance, flexibility, and connectivity.
Also consider the cost of maintenance on each equipment piece, as well as how important it is in the overall process. A peripheral component that no longer meets current needs might easily go away. But an essential machine could disrupt your entire production if it’s replaced too quickly.
And don’t forget: AX Control can help you maintain the legacy systems you choose to keep. Our vast inventory of reconditioned and new never-used OEM components can prolong the health of these systems for years. Our in-stock products ship within hours, and with expedited shipping available to most places around the globe, we can have parts to you in no time.
Machinery Manufacturing Outlook: Now and Next Year
This year has been one of recovery. Worldwide, machinery manufacturing remains held back by supply chain bottlenecks. While this situation shows signs of improving, a full recovery isn’t expected any time soon.
Demand remains, but supply prices are causing setbacks. Manufacturers are facing increasing metal costs. Yet steel prices will likely climb higher in the coming months as China cuts its output of the metal. China currently makes more than half of the world’s steel.
Specific markets within machinery manufacturing report strong 2021 sales compared to the previous year. However, these same markets seem to expect slower growth in 2022. 1 2
Talk to our team today for a personalized quote on any GE, Reliance, Fuji, or Cognex replacement part.
1 https://www.oemoffhighway.com/market-analysis/article/20839295/slower-growth-trends-likely-in-coming-months
2 https://www.aem.org/news/ag-equipment-economic-outlook-how-long-will-the-boom-continue
You must be logged in to post a comment.