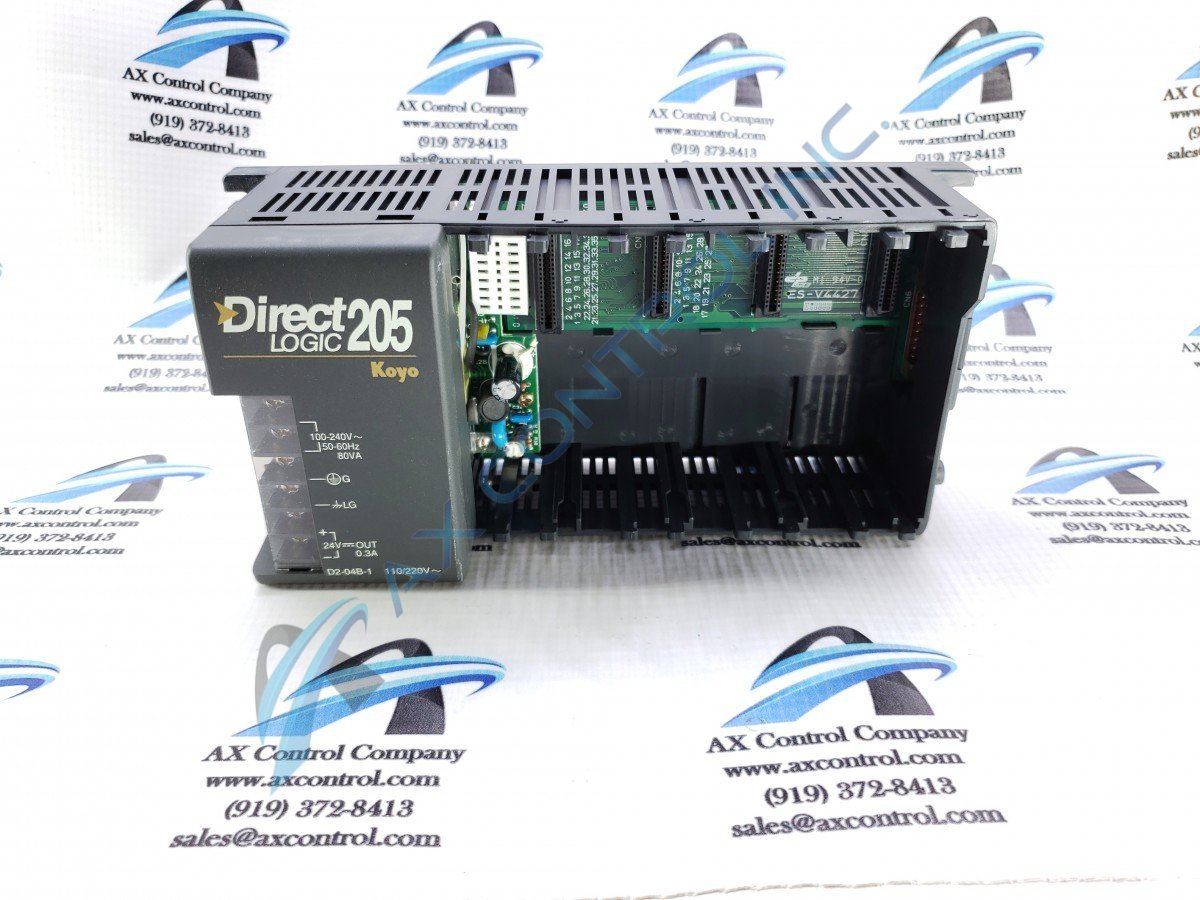
Here at AX Control, we field a lot of questions about the devices we sell. This is the first in a series of posts that will answer some of those FAQs. This post will focus on the Koyo Direct Logic 205 series.
What is the Koyo Direct Logic 205?
Automation Direct DirectLOGIC 205 controller is a micro-modular programmable logic controller. These PLCs have a built-in power supply and come in 3-slot, 4-slot 6-slot, and 9-slot versions. Certain versions of the DL205 support up to four expansion bases.
How can I load programs onto a DirectLogic 205 PLC?
Downloading a program and connecting to the Koyo DirectLogic PLC is covered extensively in the AutomationDirect manual. Here are the basic steps:
- Start the Linking Process by connecting via the PLC menu bar(first option in the dropdown menu.)
- Add a new link by clicking “Add to” in the ‘select link’ pop up menu. If you have created previous communications links the menu will give you the option to select which link you want to proceed with.
- Select a COM port. You should have previously connected a communications cable to your desired COM port. Now re-enter that COM port location into the pop-up menu and hit “Next.”
- Select a PLC family from the pop-up menu. In this case, you will choose 105/205/405 family.
- Select your communications protocol. Leave the PLC address set to the default.
You must be logged in to post a comment.