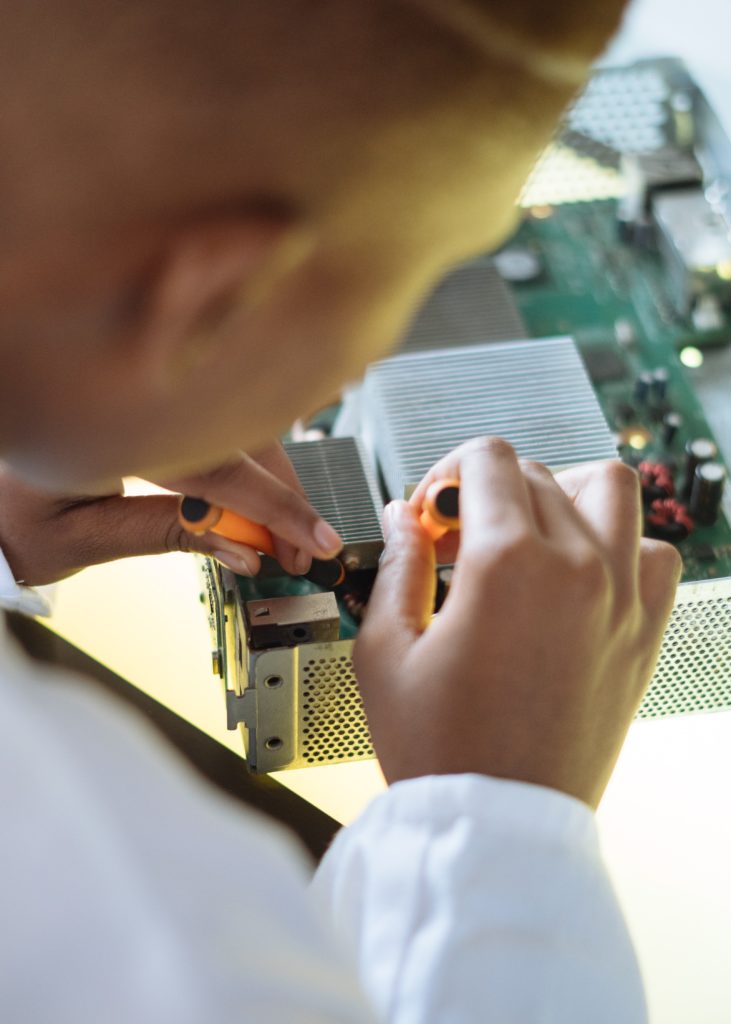
At AX Control we do a lot of repairs on motors and drives. Not only do we offer repair services for our customers, but we also examine every reconditioned part leaving our warehouse for defects and optimize its performance before it gets boxed up for transit. Our people get plenty of hands-on time with all sorts of drives and motors.
Skilled technicians take care of all our repair work. We back up that work with a 2-year warranty for AC/DC and Servo Drives, and a one-year warranty for Motors.
But do you know what may lead to your components needing repair? We get there’s a lot to know about industrial automation equipment. We thought we would offer up a list of the most common causes we’ve noticed, partitioned by type of drive or motor.
AC Drives
There have been many technological advances in the field of AC Drives that have brought more features to these drives even as they’ve decreased in size and cost.
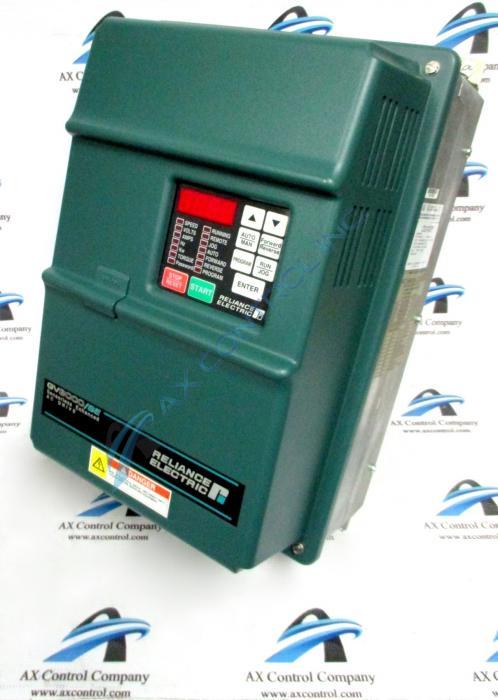
The primary driver of repairs in AC Drives, without a doubt, is heat. This may come from various sources, but when you get to the root of the problem heat is the cause of the damage.
Here are a few of the most common ways heat strikes:
- A dusty environment. When fans aren’t cleaned on a regular basis, the drive can’t pull air through, and heat builds up. Protection is easy: maintain a regular maintenance schedule and keep fans and other heat dissipating equipment clean. Try to cut down on the amount of dust in your environment through mitigation.
- Power spikes. These can come from other machines, from lightning strikes, or from your main power line. You can often limit these problems by adding a line reactor in front of your drive system to protect from transients and power surges.
- Too much power draw. If a drive is attached to a poorly-maintained motor, such as one with ungreased bearings, too much bearing wear, or shaft imbalance, this can cause a mechanical overload that increases the motor’s demand on the drive. Connected systems have to be maintained together or they will die together.
You must be logged in to post a comment.