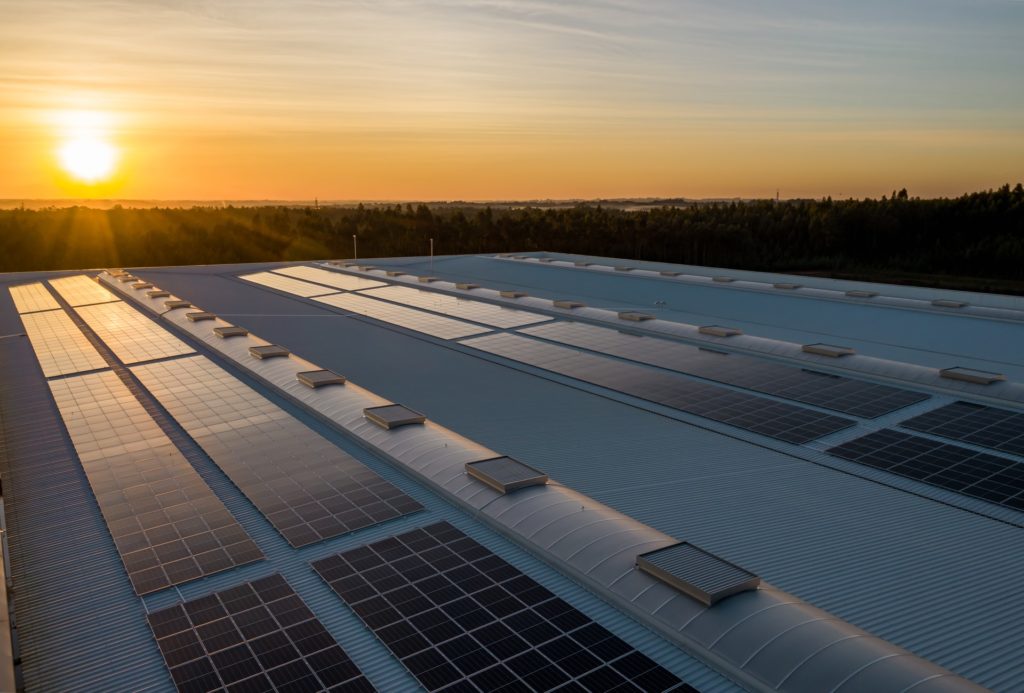
The US Energy Information Administration estimates manufacturing operations use roughly thirty-five percent of all domestically consumed energy each year. The sector uses natural gas, petroleum, coal, as well as renewable resources. This high percentage places the manufacturing industry in a unique position to make a real difference in ongoing sustainability efforts. Sustainable manufacturing is possible. But in the real world, profitability must always take precedence; an unprofitable, failing company helps no one.
Luckily, manufacturers already do a lot to mitigate energy use and expenditures. Maximizing efficiencies to meet financial goals and improve competitive advantage is part of the job. As it turns out, waste reduction and energy-efficient manufacturing practices often lead to lowered costs, creating value for both society and shareholders alike.
But more can always be done. As economic and environmental concerns mount, manufacturers are challenged to create more sustainable processes through improved optimization. Here are five steps to help with that.
Sustainable Manufacturing Tip: Eliminate Waste
In the past, manufacturers focused on production times and production costs. Both are still vital. But resource management must also play into the equation.
Reevaluate how resources are used. Consider whether it’s time to invest in precision manufacturing equipment to increase opportunities for waste reduction. Also, you can recover waste materials through techniques like filtration, electrolysis, or reverse osmosis.
Another possibility is creating a symbiotic relationship with another company. Your waste may be a resource they need. This sort of industrial symbiosis is an excellent way to decrease waste in a win-win manner. This option can offer significant savings through cost-sharing. Additionally, the sustainability advantages of closed-loop supply chain management are becoming increasingly important to younger buyers. As B2C companies are pressured by consumers to improve supply chains, so too will suppliers.
Improve Fossil Fuel Use or Switch to Green Options
The more energy used, the more costs escalate. Manufacturers have several options to reduce traditional energy costs.
A large energy cost stems from lighting. And yet, it’s surprising how often areas remain lit even when unoccupied. Incorporating automated lighting systems with motion detectors will limit how long areas remain illuminated when no workers are present. Additionally, LED lights can decrease energy consumption during use.
Another way to reduce energy consumption is by performing regular equipment maintenance and cleaning. Dirt, dust, and accumulated oil or grease acts as a blanket on your equipment, raising its temperature. This forces it to work harder, drawing more energy. Not only will regular maintenance improve energy efficiency, it will also help optimize component performance and lifespan.
Well-maintained machinery can waste energy, too. Install automatic shut-offs that will power down idle machines. If you’re unsure of when idle times occur, use data logging in a historian to report and analyze energy use. Also, consider replacing equipment with more energy-efficient machines. A variable speed drive or variable frequency drive will use less energy than a similar single-speed, for example.
Don’t rule out green energy options, too. Manufacturers around the world are now considering options like biogas, wind, and solar, with some larger corporations like General Motors now sourcing almost one-third of their power needs from green energy. But even something as simple as planting trees on the sunniest side of your facility to reduce heat transfer may produce significant savings. Green options don’t have to mean “big investment.”
Sustainable Manufacturing Tip: Recycle
Most manufacturers run some sort of recycling program. But long-time in-place programs that haven’t been updated will have become inefficient for your current needs. Regular observation of discards and how to best separate this material out of your waste stream is a good first step. This can also help you identify unnecessary waste.
Mindful sorting should be a significant part of any recycling program. Managing waste so it is densified and ready for hauling helps minimize space requirements. Some of your waste products may be organic in nature, creating the possibility of converting waste into reusable compost or biomass.
Finally, consider recycling your older components when it’s time to upgrade. Oftentimes, other manufacturers may need those parts to keep their existing systems running. Suppliers like AX Control will offer to purchase your well-maintained stock as a source for replacement parts for others. Double your sustainability power punch by buying secondhand surplus replacement parts, too.
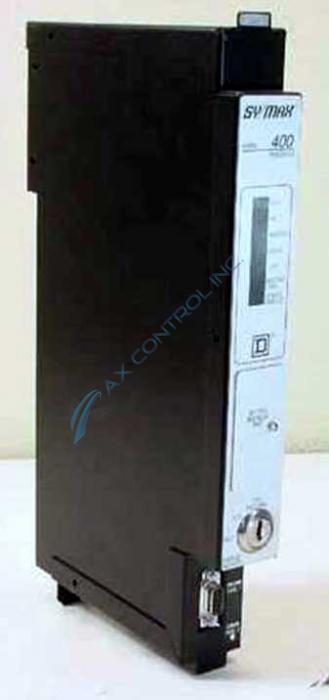
If you’re not running a recycling program, consider touching base with local recycling organizations as a first step. Many offer free counseling and can provide detailed and specific advice for your facility.
Shorten Production Cycles
Time savings alone is a type of energy savings. But if a production cycle can be completed in less time without additional energy consumption, shutdown can occur earlier, saving energy. It can also lower other associated costs like labor costs, leading to higher profit margins, lower product prices, and an improved competitive advantage.
Sustainable Manufacturing Tip: Reduce Pollution
Rather than run cutting tools with mineral oil, consider environmentally-friendly vegetable-based options. These metalworking oils often maintain fluid longer due to low viscosity and have higher flash points than traditional oils. This, in turn, can improve worker safety through reduced fire risk.
Deburring processes offer another way to reduce shop pollution. There are dozens upon dozens of ways to remove manufacturing blemishes, from hand deburring to high-temp deburring. However, they can be detrimental to the environment.
Most deburring options affect the surface finish. Almost all will change part dimensions. The best option is to prevent or minimize burrs whenever possible through smart part design or down milling. Where deburring is necessary, work to achieve your objective with the most ecologically friendly option available. This may require research to find what works best for your needs.
Conclusion
Sustainability doesn’t have to be a synonym for expensive. So many sustainability practices are also common sense good business practices that will, in the long run, save money. Installing full-scale solar production on-site might be great, but it’s not practical for everyone. But focusing on the small, everyday changes can add up in a positive way for both the environment and your pocket.
Interested in sourcing surplus or secondhand industrial automation parts? We can help! Talk to our team today.
You must be logged in to post a comment.