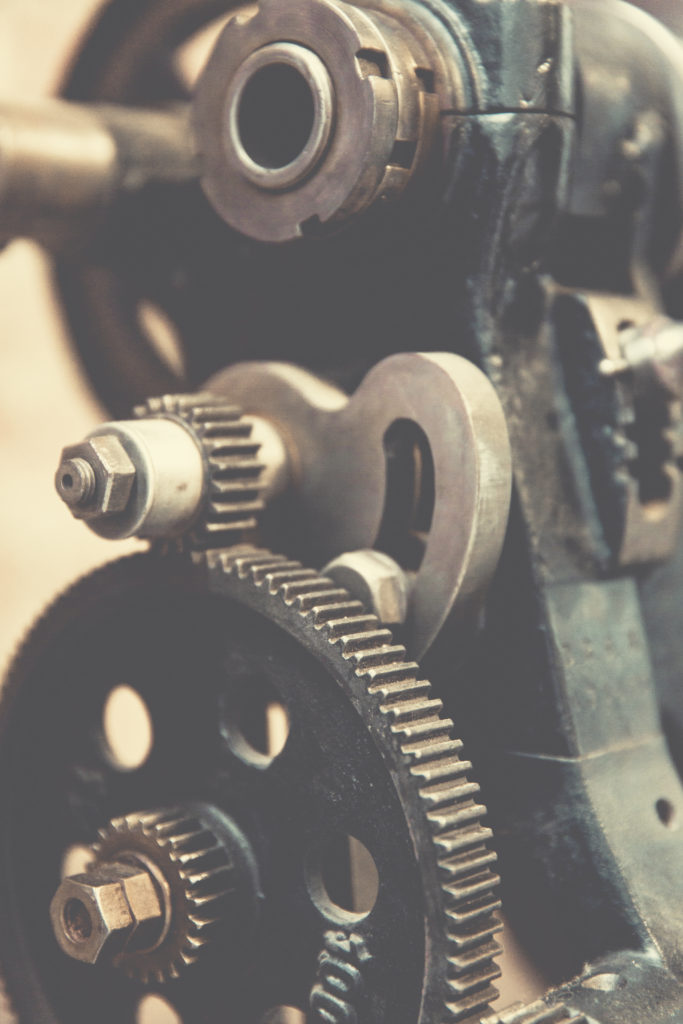
Unplanned downtime due to equipment obsolescence.
It’s a dirty subject no one wants to talk about. And for good reason. A 2016 study by the Aberdeen Group put downtime costs across industries at a whopping $260,000 per hour, up 60% from 2014 data. A 2014 Gartner study was even worse: placing the average cost at $336,000/hour. One lost eight-hour shift could mean a $2.08 million to $2.68 million loss.
Regardless of who’s right about the costs, eliminating downtime and disruption is a high priority for most businesses. Yet more than two-thirds of companies don’t have a full understanding of when their equipment should be maintained, upgraded, or replaced.
While we’re excited about the future of Industry 4.0 and IIoT, where every machine can self-analyze its needs and tell you what to do before there’s a problem, we also understand most factories and industrial locations aren’t there yet. They likely won’t be for decades as they continue to operate with older systems in place.
But old doesn’t mean unusable. Here’s why.
Continue reading “How To Manage Equipment Obsolescence”
You must be logged in to post a comment.