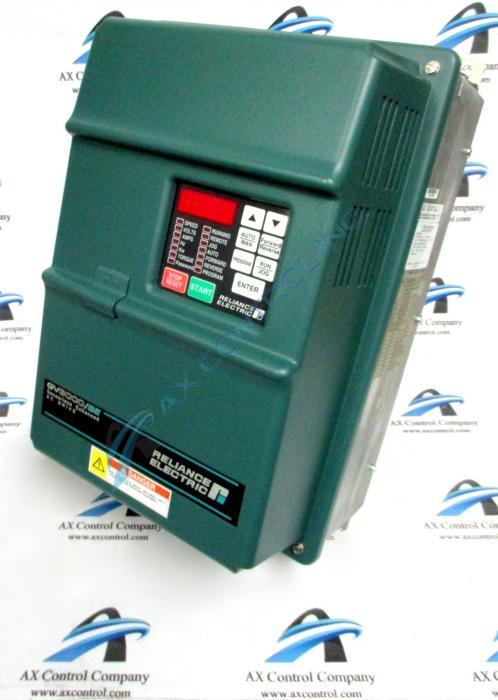
Reliance VFD drives have been around for years. VFDs have been widely used for industrial applications, for good reason. Pulse-width modulation (PWM) VFDs offer low costs, high efficiency, and excellent input power factor.
However, VFDs need proper care and installation to run optimally. Sometimes this means controlling airflow going to the drive to control heat generation. VFDs have a typical efficiency rating between 95-98%. But VFDs produce more heat than other electrical equipment, especially when enclosed. And heat losses are directly related to the VFD’s efficiency rating.
Make sure to note your drive’s max operating temperature under real operating conditions. Some drives can operate to 122 degrees Fahrenheit safely. Others can only withstand max temps of 104 degrees Fahrenheit before overheating. To extend the life of your equipment, err on the side of caution and try to operate VFDs below their rated max operating temperature. This will extend your equipment’s lifespan. It will also reduce any risk of localized overheating.
Positioning is Key
One way to ensure your Reliance VFD maintains temperature is through proper positioning. Try to place VFDs close to the bottom of electrical enclosures. This will ensure incoming air is as cool as possible, since it hasn’t already run across other components. Also, maintain recommended right-to-left clearances between units.
Why Are VFDs Used?
Many prefer VFDs like the Reliance VFD over single-speed drives because they can control the speed of an AC motor while offering smooth startup capabilities. Adjustments to frequency delivered to the motor prevents straining from heavy load.
VFD Design Saves Energy
This same frequency adjustment offers energy savings, too. VFDs allow motors to operate at less than full speed. A 25% reduction of motor speed can decrease energy consumption by close to 60%. Meanwhile, a 50% reduction can decrease consumption by almost 90%.
It is important to note “frequency adjustment” can also fall under the misnomer of “speed control.” Speed control is the result of the former. As downward adjustments in frequency occur, other improvements follow improved energy consumption. Mechanical stress lowers, extending machine lifetime. Noise levels also reduce.
Where are VFDs Used?
Three out of every four VFDs produced end up as part of control systems for pumps, fans, and compressors. It is easier to control the speed of a pump through a VFD rather than try to control the flow of water or air in the system through valves. This makes VFDs perfect for pump and fan applications.
Need replacement parts for your Reliance VFD? We can help! Talk to our team today.
You must be logged in to post a comment.